Exploration Below the Surface |
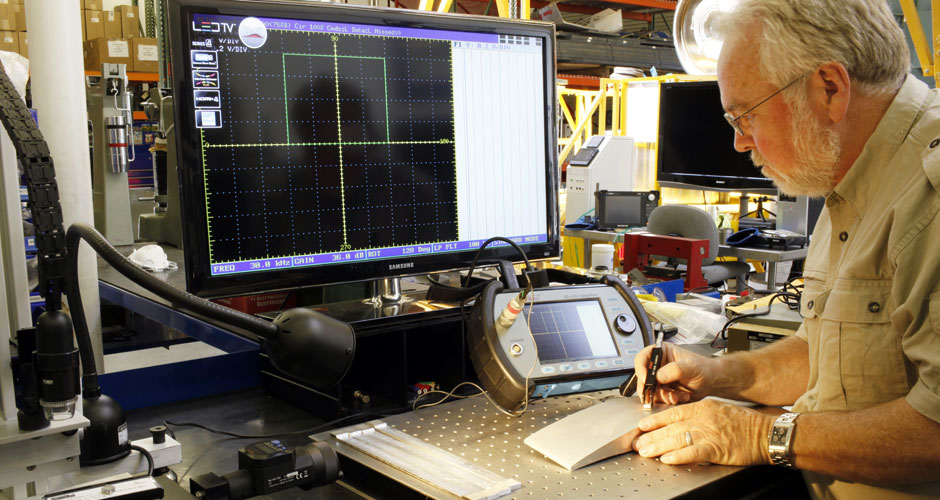 |
Eddy Current Electromagnetic Induction
Eddy Current testing is widely used in the aerospace industry and in other manufacturing and service environments that require inspection of metals for potential safety-related or quality-related problems. In addition to crack detection, Eddy Current can be used for certain metal thickness measurements such as identifying corrosion, to measure conductivity and test for heat treatment of parts.
Eddy Current NDT can examine large areas very quickly, and it does not require use of coupling liquids. In addition to finding cracks, Eddy Current can also be used to check metal hardness and conductivity in applications where those properties are of interest, and to measure thin layers of nonconductive coatings like paint on metal parts. In some cases, eddy current and ultrasonic testing are used together as complementary techniques, with eddy current having an advantage for quick surface testing and ultrasonic's having better depth penetration.
How It Works
Eddy Current testing is based on the physics phenomenon of electromagnetic induction. In an eddy current probe, an alternating current flows through a wire coil and generates an oscillating magnetic field. If the probe and its magnetic field are brought close to a conductive material like a metal test piece, a circular flow of electrons known as an Eddy Current will begin to move through the metal like swirling water in a stream. That eddy current flowing through the metal will in turn generate its own magnetic field, which will interact with the coil and its field through mutual inductance. Changes in metal thickness or defects like near-surface cracking will interrupt or alter the amplitude and pattern of the eddy current and the resulting magnetic field. This in turn affects the movement of electrons in the coil by varying the electrical impedance of the coil. The eddy current instrument plots changes in the impedance amplitude and phase angle, which can be used by a trained operator to identify changes in the test piece. |
|
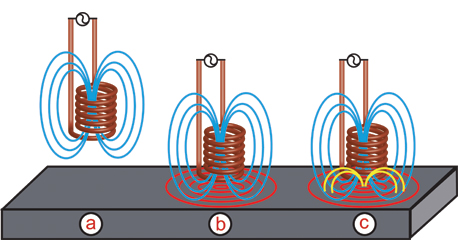
|
( a ) |
The alternating current flowing through the coil at a chosen frequency generates a magnetic field around the coil. |
( b ) |
When the coil is placed close to an electrically conductive material, eddy current is included in the material. |
( c ) |
If a flaw in the conductive material disturbs the eddy current circulation, the magnetic coupling with the probe is changed and a defect signal can be read by measuring the coil impedance variation. |
|
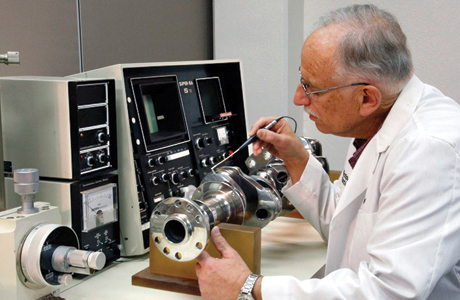 |
|
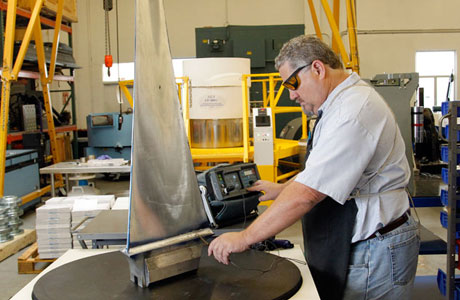 |
Eddy Current Inspection on Crankshaft |
|
Eddy Current Inspection on Turbine Blade |
|