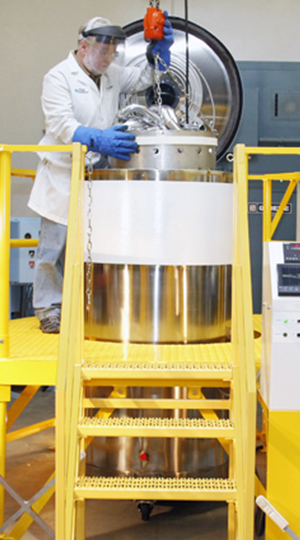 |
|
Cryogenic Liquid Nitrogen Stress Relieving
Metal Stress Relieving using –300F Cryogenic NDT Testing

Cryogenic Non Destructive Testing & Material Treatment
Patent Approved Number: US 2014/8,920,023 December 30, 2014
Cryogenic Transition Detection
Patent Approved Number: US 2014/8,894,279 November 25, 2014
Piston aircraft engines are quite different from most automobile engines as they rely entirely on available air-cooling to control engine oil and parts temperatures. Engines are exposed to significant changes in temperature as a result of changing airflow and rapid expansion and cooling of the engine parts occur. This can cause premature engine parts failure, reduction of power and oil leaks to occur.
Because aircraft engines are subjected to this rapid expansion and contraction of engine parts any residual stress that is in the engine parts can significantly affect the life of an engine. Residual stress occurs in parts at rest, and is a by-product of manufacturing processes and cyclic use. For a technical description of residual stress please see (Note 1.)
To reduce residual stress in parts, Victor Aviation uses a FAA accepted process –300F Cryogenic Non Destructive Testing (NDT) for stress relieving the parts. After parts have been stress relieved the parts are less susceptible to premature failure, become more durable, stable, and longer engine life can occur.
Patent Approved
|
Engines Parts Inspected for Surface Geometry Change
To best demonstrate this stress relieving process we placed a new perfectly machined engine crankcase on a grade A Granite Surface Plate and documented that the parting halves were perfectly flat. After the crankcase went through the –300F Cryogenic NDT Process it was then again placed on the same surface plate and measured again. It was found that the crankcase geometry then shifted to its relaxed or stress relieved state and was found to have twelve thousandths on an inch deviation in surface flatness across the parting surface.
If this same crankcase were to have been installed in an engine without being stress relieved, over a period of time as the part was subjected to expansion and contraction in normal use, this residual metal stress could attempt to shift the part geometry to its relaxed metal state. This could cause crankcase cracking; uneven pressures on the engine bearings, increased engine friction, reduction of power and oil leaks to occur.
As a comparison, after we re-machine a crankcase that showed signs of stress relieving by a change in geometry after the –300F Cryogenic NDT Process was applied, the part will remain flat and not distort during normal engine operation from residual stress as it is in its relaxed metal state. The result can be a reduction in case cracking susceptibility, even crankcase bearing pressures, decreased engine friction, improvement in power and improved fatigue life of parts.
|
Time, Temperature and Cycles of Use
When a new part is installed in an engine sometimes a part may fail prematurely for no explained reason, even after it was properly installed and passed proper inspection. This is what is called “Infant Mortality”. Basically what happens is that the part didn’t hold up while it was going through normal use while being exposed to time and temperature changes, vibration and cyclic use. Unfortunately unless a part has been through a long period of these cycles it can be susceptible to fatigue failure resulting from residual stress and other forces applied to the part.
Ironically, over a very long period of time as parts are exposed to temperature changes, vibration and cyclic use, residual stresses can be reduced. This is why your Grandpa may have said: “They just don’t make engines the way they used to”. What Grandpa was referring to is that he had an engine that lasted forever and never had a problem. Perhaps this was his tractor or truck engine that he used in the Midwest. When he observed an engine that was built new today it just didn’t last and had an early parts failure.
What really happened with Grandpa’s engine was that the engine’s residual parts stress became relieved over time with cyclic use and lasted forever, while enduring many seasons of hot summers and freezing winters.
What Grandpa had achieved with his engines parts life over a period of many years or decades from sustained engine operation and seasonal temperature changes, we achieve similar results of improved parts durability and stability using -300F Cryogenic NDT processing.
This same stress relief principle applies to not just crankcases, but to crankshafts, camshafts, connecting rods, engine gears and any other stressed or mated metal engine parts. |
|
Through many decades of climate changes, new engine parts become more stable and last longer. Victor can achieve new parts stability in
just a few days. |
|
Cryogenic Engine History
Cryogenic Processing of aircraft engine parts dates back to the 1930’s and was reportedly used by the Hugo Junkers Aircraft Company on their Jumo 1,000 HP V-12 aircraft engine developments. These engines were installed in many German Air Force Fighter Aircraft such as the Messer Schmidt ME209 and JU87 Stuka Bombers used as primary aircraft in World War II.
Today, Cryogenics Processing is widely used by the Aerospace Industry, NASA, Jet Engine Manufacturers, Automotive Industry, Nascar Engine Builders, Semi Conductor and other Manufacturing Companies for improving parts durability, stability and engine performance.
With the assistance from some of the nations most educated and experienced engineers, including the former X-15 Rocket Pilot and Propulsion Engineer Scott Crossfield, Metallurgists and PhD Physicists from the Massachusetts Institute of Technology and Universities, Victor Aviation has now introduced the Patent Approved –300F Cryogenic NDT Process.
|
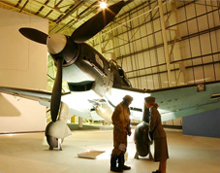 |
|
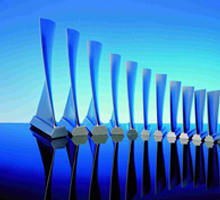 |
|
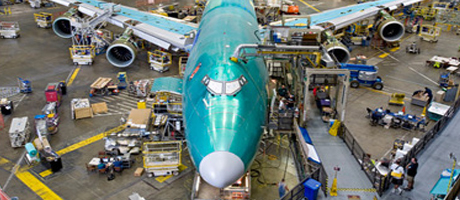 |
Cryogenic in History |
|
Gas Turbine Compressor Blades |
|
Boeing 747-B Freighter |
Performing the –300F Cryogenic NDT Process takes very specialized equipment with highly skilled technicians. The parts to be processed tested will first go through a complete NDT test procedure to inspect the quality of the parts. The geometry of the parts are then measured and a baseline will be established for the parts to be Cryogenic NDT tested.
The testing process takes place over a period of several days and is controlled by a computer that is programmed for a very slow rate of temperature change, and establishes the duration of temperature event cycles.
Once the Cryogenic Chamber has returned to room temperature following the cryogenic cold cycle, a heat cycle is also executed on some parts applications and finally returned to ambient room temperature all under the control of computer programming.
Parts are then removed from the Cryogenic Chamber and the initial NDT tests that were performed on the parts are all performed for the second time.
Parts Geometry is also measured again and the test data will be compared to the initial data that was recorded prior to NDT Cryogenic Process testing.
Should any part dimension change following the Cryogenic NDT Test process and are found out of dimension specifications, they will either be re-machined to proper specifications or replaced with another NDT stress relieved part meeting correct dimensional specifications.
Not only has this Non Destructive Testing Process proven to allow Victor Aviation technicians to determine residual stress of aircraft parts, it has allowed Victor to further evaluate the longevity of parts and create a better product. |
|
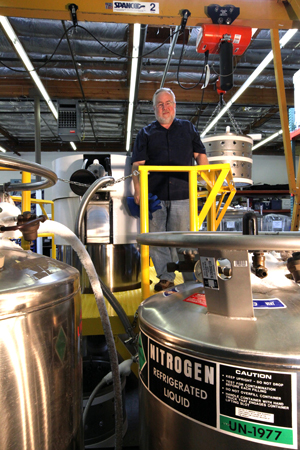 |
|